How FutureDial and Dis-Connect are shaping the future of automated device processing
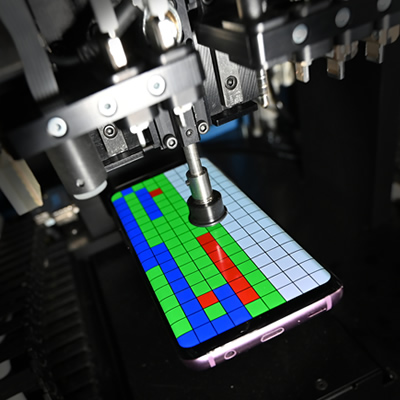
As summer came to an end, we set off to Karlsruhe, Germany, to see firsthand how Dis-Connect is leveraging FutureDial’s cutting-edge automation solutions. FutureDial, a leading global company specializing in automated device processing, has made its mark in the secondary electronics market by providing efficient and scalable solutions. The goal of our visit was to explore how these technologies are being implemented in a European context, and we were joined by FutureDial’s Simon Harrison, Vice President Strategic Accounts EMEA, and Georg Dis, CEO of Dis-Connect, who offered invaluable insights over a relaxed coffee meeting.
For those unfamiliar, Dis-Connect operates as a key player in the European refurbished electronics market. Their mission is to provide high-quality circularity and refurbished devices, helping to bridge the gap between rising consumer demand for affordable technology and sustainability goals. As Europe pushes toward a more circular economy, innovations like those from FutureDial are essential to ensure seamless, efficient, and scalable processes for refurbishing and reselling used devices. To speed up this process Dis-Connect and FutureDial are joining forces in Europe, merging machines, software and streamlining operational processes by developing a joint center of excellence and a combined HQ in Karlsruhe.
Efficiency at its best: FutureDial’s automated processing machines
The focus of the visit was to observe FutureDial’s equipment at work. At Dis-Connect’s state-of-the-art facility, five automated testing machines and one grading device had recently been installed. According to Simon Harrison, this setup represents the next frontier in automated testing, data wiping, and grading of pre-owned devices. Each of these machines can process over 500 smartphones per day during a single shift, significantly boosting the facility’s capacity to handle large volumes.
The process is highly streamlined. Each device undergoes a series of tests, checking it on over 90 different criteria, including screen performance, battery health, camera functionality, and more. The system also ensures that each device is fully data-wiped both before and after testing, adhering to stringent data security protocols. The entire process is tracked by the device’s IMEI number, providing a detailed report on the condition and performance of the phone.
Testing a typical Android smartphone takes three minutes five seconds, while Apple’s iPhones are tested in just under two minutes and fifty seconds—a remarkably quick turnaround time for such thorough diagnostics. Simon Harrison emphasized the efficiency of the setup, noting, “One person can easily handle five machines simultaneously. However, as we continue to scale, there’s an opportunity to further automate the process. Adding robotic arms and a conveyor belt would greatly increase throughput, allowing us to process even more devices with minimal human intervention.”
Testing a typical Android smartphone takes three minutes five seconds…
The Role of AI in Automated Grading
One of the highlights of the visit was FutureDial’s advanced grading machine, which plays a crucial role in determining the resale value of each device. As we entered the processing area, the size and sophistication of the grading machine immediately caught our attention. Simon Harrison smiled and quipped, “Impressive, isn’t it?” Indeed, the machine was undergoing calibration at the time of our visit—a meticulous process that underscored the level of precision FutureDial’s technology brings to device grading.
As part of the calibration, the grading machine ran into an interesting hiccup: it flagged a European model iPhone 15’s SIM tray as a scratch. This is a good example of how the AI-powered system continues to evolve. European models of the iPhone 15 come with a physical SIM tray, unlike their U.S. counterparts, which rely solely on eSIMs. The machine mistook the SIM tray for a defect, but this issue was quickly rectified, showcasing how machine learning improves accuracy immediately.
Harrison pointed out, “While FutureDial already boasts one of the highest grading accuracies in the industry, it’s not 100% perfect yet. As the AI continues to learn and calibrate, we’re constantly improving the precision of our grading technology.” Dis-Connect has also taken FutureDial’s solution a step further by developing its own AI-based grading software add-on, which enhances the accuracy by analyzing multiple photos of the device taken during testing. “This additional software layer allows us to push accuracy even further, making our grading process more reliable,” said Georg Dis.
This level of accuracy is crucial in the secondary electronics market, where even small imperfections can impact the resale value of a device. Currently, FutureDial offers over 20 different grading policies, which are all full customizable to specific requirements, and the system can intelligently decide whether a device can be polished to improve its appearance or if doing so would cause more harm than good. “The key is to know when buffing will upgrade the grade of a smartphone and when it’s better to leave it as is,” added Dis. “Our system helps our customers make those decisions quickly and effectively.”
Streamlining the entire process
The journey of each device at Dis-Connect begins at the SMART Receiving desk. Here, devices are connected to the system, fully data-wiped, and checked for various locks, including FMI (Find My iPhone), MDM (Mobile Device Management), SIM locks, and whether the phone has been reported as stolen. Once the initial checks are completed, FutureDial’s test application is installed on the device.
The installation of the app is crucial for the automated testing phase, as an operator grants access to all of the phone’s core functions—Bluetooth, microphones, speakers, NFC, and Wi-Fi—for further comprehensive testing. The phones are charged to a minimum level if needed, ensuring they are ready for the test process. After this, the operator places the smartphone in FutureDial’s fully automated SmartTest machine. Using a barcode system, the machine begins a predefined series of tests tailored to the specific make and model of the device.
Once the testing is complete, the results are displayed for the operator, indicating whether the device has passed or failed. In the case of a failure, the specific reasons are clearly shown, enabling the operator to take appropriate action. If the device passes, the final step is a second, thorough data wipe to ensure all personal data is removed. As Harrison noted, “You want a device to power up with a clean slate welcome screen. That’s why this final data wipe is essential”.
At this point, the fully tested and graded devices are ready for packing and shipping to customers. This streamlined process has enabled Dis-Connect to consistently deliver high-quality, certified pre-owned devices to their clients, which include leasing company Grover and German telecom operator Freenet.
The future of automated processing in Europe
Walking through Dis-Connect’s impressive facility, Georg Dis remarked, “FutureDial’s solution is extremely versatile and fits perfectly into our processing workflow. Two of our major customers wanted consistency in grading and optimization in our processing, and with the support of FutureDial, we’ve been able to meet these demands.”
By integrating FutureDial’s technology, Dis-Connect has minimized risk and maximized operational efficiency, helping to ensure that devices are processed consistently and reliably. The facility is now well-positioned to meet the growing demand for refurbished electronics in Europe, driven by both consumer preference and sustainability initiatives.
The combination of AI-powered grading, automated testing, and scalable processing makes FutureDial a key player in the future of the European secondary electronics market. As more companies in Europe embrace these technologies, the potential for growth in the refurbished smartphone market will only increase, bringing high-quality, affordable devices to more people while contributing to a more sustainable tech industry.